R&D – FINITE ELEMENT ANALYSIS (FEA)
What is the finite element method ?
The finite element method (FEM) is a numerical method that simulates the behavior of a complex elastomeric product in the face of the actions it will have to face (forces, vibration, heat, etc.).
This method makes it possible to create finite element models as close to reality as possible. In this calculation, the different materials and the environment of the system are taken into account.
The finite element calculation is used during the development of the elastomer product and guarantees a response in accordance with the specifications.
What are the steps of the finite element calculation ?
The calculation by finite elements takes place in several stages :
- From the CAD (Computer Aided Design), which itself comes from the customer’s input data, the design of the elastomer product is integrated into the calculation software.
- Entering the criteria of the internal and external environment of use of the elastomer product (from the customer input data).
- Launching of the finite element calculation.
- Obtaining the results : this calculation must confirm whether the design is compliant or not.
Delmon Group is a global solution designer with adapted manufacturing processes.
Fully integrated, from the formulation of its elastomers to the validation of molded parts. The company offers you the benefit of all its know-how and engineers skills to respect your specifications.
THE R&D TEAM IS ABLE TO WORK WITH THIS FOLLOWING SOFTWARES :
CATIA : Parts design by CAD (Computer Aided Design)
ABAQUS : Nonlinear FEM meshing and calculation (finite element calculation software)
PROTOTYPING / MEASURES / TESTS
What is prototyping ?
Prototyping is a method that allows us to remove doubts about a theoretical design by producing a small series of parts, in our case, in rubber. At the end of the customer’s tests, it allows to confirm or not the technical feasability of the part. This prototype allows us to identify problems and correct them if necessary. This step occurs before launching the part in series.
Our skills in prototyping…
Delmon Group has a workshop dedicated to prototyping, measurements and endurance tests. The workshop allows the company to be reactive in developing different solutions/ concepts with customers.
These prototyping processes provide an optimal reactivity to meet the demands of Delmon Group’s customers.
FORMULATION
THE DELMON GROUP ELABORATES AND REALIZES ITS FORMULATIONS IN-HOUSE FROM YOUR NEEDS.
SPECIALISTS ARE AT YOUR DISPOSAL IN PHYSICAL CHEMISTRY LABORATORIES
- To create new formulations or improve them.
- To help you approve mixtures for your own customers.
- To carry out counter-expertise of mixtures.
The mixture formula is established from a precise specification, respecting criteria such as hardness, color, mechanical properties, chemical resistance, fire resistance, etc… in accordance with the regulations and the analysis of the function of your product.
Delmon Group’s chemists teams are recognized through customer certifications, such as :
Renault,
Safran,
GE Aerospace, etc…
MIXING
Delmon Group produces an important part of its rubber through its mixing lines using laboratory formulations.
BONDING
Key Competence : Bonding
Bonding is achieved in most cases by surface preparation adapted to the insert material and the rubber formula.
There is a specific adhesive for each elastomer family.
Adhesion occurs as a result of vulcanization in the mold.
Bonding is a proven know-how of Delmon Group’s skills and is design based on your applications and specifications.
MOLDING
What is molding ?
Moulding is a technique that allows the production of a part through the insertion of a material in a mould. It allows us to produce complex rubber parts.
Delmon Group’s moulding skills
WITH MORE THAN 50 YEARS OF EXPERIENCE, DELMON GROUP IS A SPECIALIST IN THE MOULDING OF RUBBER PARTS.
The company has a large number of injection, compression and transfer presses. It realizes the overmoulding of adhered parts with plastic and metal inserts.
Its machine park is mainly composed of presses from 17T to 600T with bowls that can contain up to 6L of mixture. The group has the necessary skills to mold and overmold small to very large parts. Presses are also dedicated for silicones.
Delmon Group designs its molds and validates them. Its presses have ejection systems with rotating frames and can be equipped with robots.
Delmon Group has injection blow molding machines for thermoplastic materials. This is a process that allows the production of complex shaped parts with hollow bodies such as bellows. This know-how has been in existence for about 20 years.
Delmon Group also produces parts with the polyurethane casting technique to meet certain specifications.
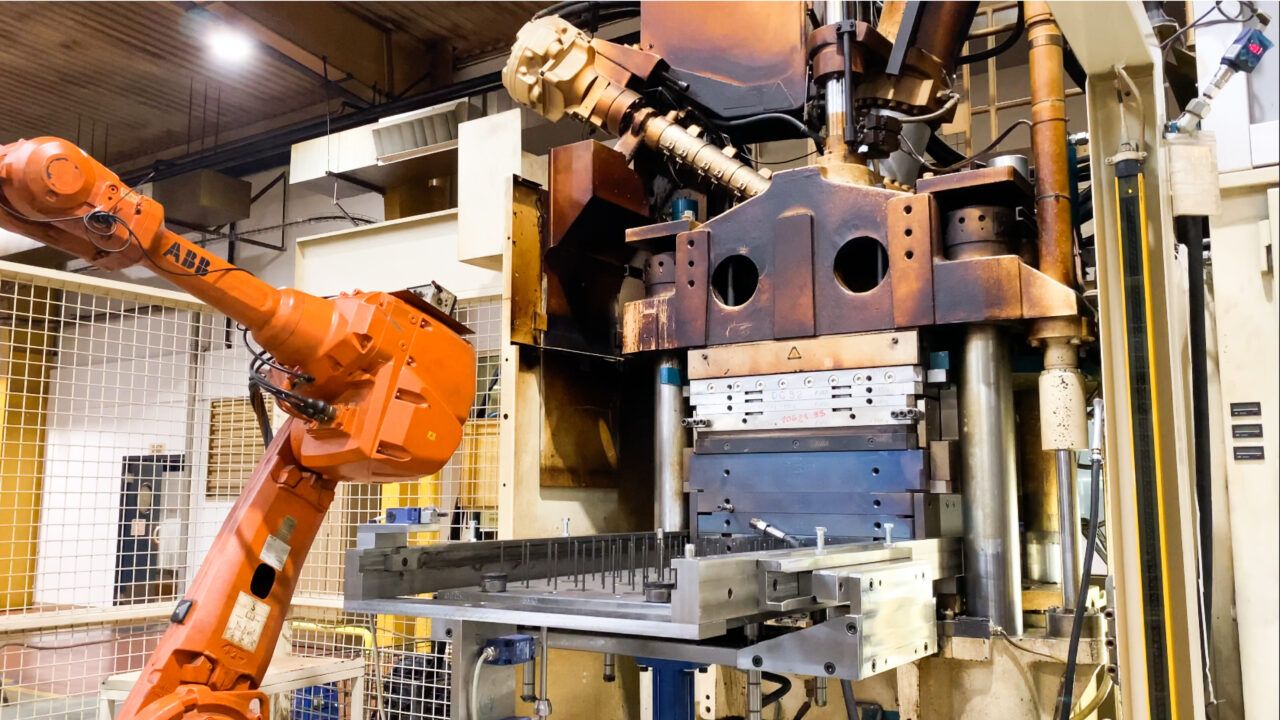
AUTOMATION
What is automation ?
Automation is the replacement of certain human tasks by robots. This technique reduces the workload of an operator and increases productivity for large series.
Our competences in this field…
DELMON GROUP INTRODUCED ITS FIRST ROBOTS FOR INSERT LOADING AND DELMOULDING OF ITS RUBBER PARTS ABOUT 30 YEARS AGO.
Over the years, automation has continued at all stages of production (gluing, moulding, finishing…)
The industrialization department defines the automated systems and also relies on the skills of integrator of special machines.
MACHINING
What is machining ?
Machining is a manufacturing method called substractive. It consists of creating parts by removing material from the part using cutting tools.
Most of time today, machining is done in « computer numerical control » (CNC).
What are the stages of machining ?
- Desigh of a CAD model (Computer Aided Design) of the part
- Transformation of the CAD fil into a CNC program and configuration of the machine
- The machine executes the CNC program
Delmon Group’s competences
DELMON GROUP HAS A MACHINING UNIT FOR INSERTS AND RE-MACHINING OF MOULDED PARTS MAINLY FOR THE AERONAUTICS MARKET.